環境配慮型工場「D's SMART FACTORY」の実証と商品化エネルギー最小化をめざす次世代省エネ工場
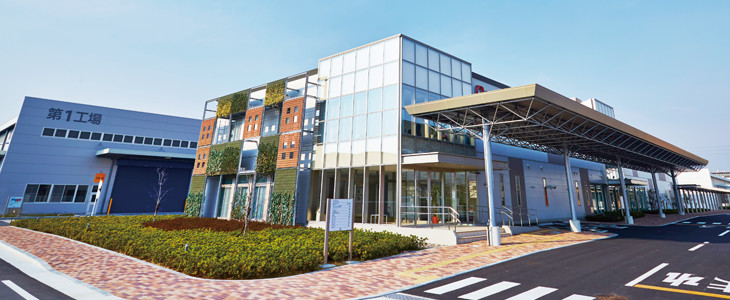
CGO(環境担当役員)のリーダーシップのもとに進めた「次世代省エネ工場の商品化に向けて~自社工場でのエネルギー最小化(MIN)への取組み~」が評価され、平成25年度「省エネ大賞(省エネ事例部門)」で最高位となる『経済産業大臣賞※1(CGO※2・企業等分野)」を受賞しました。
- ※1 同賞初となる2年連続受賞
- ※2 Chief Green Officerの略。経営の視点から事業全体を俯瞰して、省エネルギー活動・環境管理を統括する責任者のこと。
現場改善と「見える化」導入による省エネ推進
2011年に策定した「環境中長期ビジョン2020」に基づき、2020年までに自社工場の売上高あたりのCO2排出量を2005年度比50%削減を目指す「Smart-Eco Project」を推進しています。 工場においては、2005年度よりSTEP 0の活動を開始し、2012年度※2の工場全体(全10工場)の売上高あたりのCO2排出量は2005年度比48%削減※、省エネモデル工場である九州工場では同64%削減※2しました。現在は、STEP 3のステージで、さらなる省エネに取り組んでいます。
- ※ 省エネ大賞の応募資料に合わせた表記を記載しています(2013年度、工場全体で売上高あたりCO2排出量は2005年度比48%削減、九州工場で同62%削減)。
STEP 0 現場力による省エネ
STEP 0の活動開始当初は、生産現場が中心となり、燃料改質装置の導入、工場で最もエネルギー消費が大きい電着塗装ラインへの常時攪拌不要塗料の採用、電着塗装そのものが不要となる新しい工法の採用(右図)などにより、省エネ成果を上げました。ただ、改善が一巡すると、現場のやりつくした感で、成果が伸び悩みました。
新開発した「かしめ工法」「リベット工法」での接合に切り替え、電着塗装・乾燥工程を不要にしました。
STEP 1~2 「見える化」による省エネ
新機軸を求め2008年にエネルギーの「見える化」を導入。休憩時や就業後のムダなエネルギー使用などを見つけ、削減を進めましたが、大きな成果にはつながりませんでした。そこで、2010年には生産現場+工場省エネメンバー+本社部門によるプロジェクトを組み、改善を再スタート。情報共有でアイデアが広がり、大きなエネルギー削減につなげることができました。
インバータを設置するだけでなく、周波数減速時間を設備ごとに細かく調整し、省エネ効果を最大化しました。
「見える化」から「見せる化」へ、全員参加型でエネルギー最小化に取り組む
STEP 3 「見せる化」による情報共有の拡大
2012年には積み重ねたノウハウをもとにメーカーと共同開発した工場エネルギー・マネジメント・システム「D’s FEMS」を九州工場に導入し、情報の「見せる化」を実現しました。
2013年度は奈良工場にも導入し、全員参加型の省エネ活動を推進しています。エネルギーの消費状況や設備異常などがリアルタイムにわかりやすく大画面に表示され、目を向けた人が異変に対し、すぐにアクションを起こすことができます。
「D's FEMS」は、改善活動における議論に不可欠な客観データの提供ツールとしても、積極的に活用しています。
「D's FEMS」はリアルタイムの異常時対応をサポート。例えば、現場で設備異常が起こると「D's FEMS」がアラームを発し、いち早く異常を把握し、アクションを起こせます。また、同時に表示される複数のデータから、より多くの気づきが生まれます。
「D's FEMS」は過去データや電力使用状況からデマンド予測をリアルタイムで行います。予測が設定値を超えると、関係者へ自動メールするだけでなく、不要不急の照明を自動消灯したり、影響の小さい設備出力を自動調整します。
工場長の声
ものづくり・人づくりにこだわり、省エネトップランナー工場を目指す。
2008年度、「エネルギーの見える化」を導入し、生産現場の情報を関係者みんなで共有することで省エネ改善につなげ、大きな成果を得ました。2013年度は、新たに「D's FEMS」を導入。当初は、気づきを与えるアラームに追われる日々でしたが、今は適切な対応がとれるようになってきました。また、気づきを省エネ改善に結びつける活動は、専門知識が必要なため、協力会社を含めた人材育成が課題と認識し取り組んでいます。九州工場は、これからも省エネ推進事業場として「ものづくり・人づくり」にこだわり、省エネトップランナー工場を目指します。
九州工場 工場長
嶋 哲司
工場長の声
省エネ活動の水平展開と、さらなる省エネの実証検証を実施。
2005年度に九州工場で開始した省エネ活動は、生産現場中心の改善活動に始まり、省エネプロジェクト活動を経て大きなエネルギー削減につながりました。その成果は、奈良工場にも展開し、2013年度の工場売上高あたりCO2排出量は2010年度比19.3%減となりました。現在は、メーカーと共同開発した「D's FEMS」で工場全体の情報共有を進め、新たな改善を積み重ねています。また、2014年1月に「D's SMART FACTORY」のモデルとして建て替えた第一工場を活用しながら、さらなる省エネ改善・運用の定着と実証検証を継続してまいります。
奈良工場 工場長
中尾 真也
今後に向けて ~さらなる省エネ施策の検証と次世代省エネ工場の提案~
工場の省エネ活動を全社、全グループに広げる一方、お客さまにも次世代省エネ工場を提案していくことは、自社工場を持つ当社の役割だと考えています。このため、一連の活動成果をまとめ、「D’s SMART FACTORY」として商品化しました。
特に「D’s FEMS」において“どのデータがどの値を超えた時にアラームを出すべきか”といった判断基準は、スマート化の核となる省エネノウハウそのものです。このため、目下、九州・奈良の2工場で実証を進めています。今後も地道に商品の完成度向上に努めていきます。
提案の柱の一つは「アクティブコントロール」。最新の設備機器により、創エネ・蓄エネ・省エネを実現します。
採光の工夫で人工照明を抑えるなど、光・風など自然の力を利用する「パッシブコントロール」も徹底追求しています。
奈良工場を「D's SMART FACTORY」のモデルと位置づけ建て替えを進めています。2014年1月に第1期工事が完了。新築建屋でエネルギー最小化に向けた実証実験を推進中です。